Choosing the right caster wheel material for your specific application is essential to ensuring optimal performance, longevity, and safety. With a variety of materials available—ranging from rubber and polyurethane to steel and aluminum—the selection process can be overwhelming without the proper information. Understanding the characteristics, advantages, and limitations of each material is crucial for making the best decision.
This guide aims to help you navigate through the different caster wheel materials and their best uses. Whether you’re outfitting a warehouse, designing custom furniture, or seeking wheels for industrial equipment, we will provide all the insights you need to choose the right caster wheel material for your needs.
Types of Caster Wheel Materials
When choosing caster wheels, it’s important to match the material with the intended application. Below, we will explore the key caster wheel materials, their characteristics, benefits, and ideal use cases.
Rubber wheels
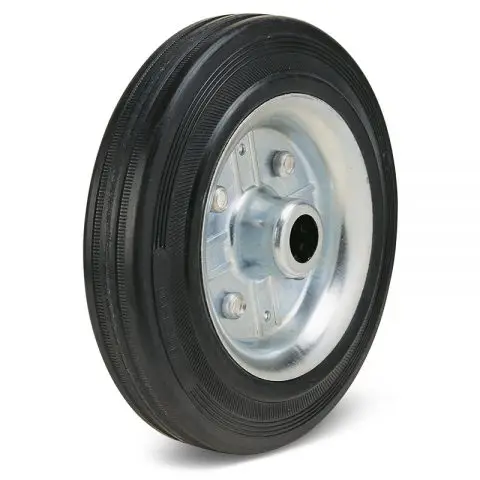
Characteristics:
Rubber caster wheels are known for their flexibility and durability. Made from natural or synthetic rubber, they are designed to absorb shock and reduce vibration. They are also quiet during operation, making them a popular choice for environments that require noise control.
Pros:
- Cushioned ride: The shock absorption capability provides a smoother ride, reducing the risk of damage to transported items.
- Impact resistance: They absorb shocks and bumps, making them suitable for environments where smooth movement is required.
- Safety Features: Excellent traction reduces the likelihood of accidents in busy environments.
- Noise reduction: Ideal for settings requiring minimal noise pollution due to their soft material that absorbs vibrations.
- Chemical resistance: Suitable for environments with exposure to harsh chemicals, enhancing longevity.
- Floor protection: Soft rubber minimizes the risk of floor damage, making it suitable for sensitive surfaces.
Cons:
- Limited Load capacity: Rubber caster wheels generally have a lower weight capacity compared to polyurethane or metal options, which can be a limitation for heavy-duty applications.
- Wear and tear: They are more susceptible to wear over time, especially on rough surfaces, leading to a need for more frequent replacements.
- Can leave marks on floors: Black rubber caster wheels typically include carbon black as a coloring agent during their manufacturing process. As a result, they tend to leave visible marks on flooring surfaces especially when used on rough or abrasive surfaces.
- Potential for flat spots: If left stationary under heavy loads for extended periods, rubber wheels can develop flat spots, affecting mobility when moved later.
- Chemical sensitivity: While resistant to many substances, certain chemicals can deteriorate rubber over time, reducing its lifespan.
Best Uses:
Rubber caster wheels are best suited for applications where floor protection and noise reduction are priorities, such as office furniture, retail environments, industrial applications, food service industry, event equipment, and home use.
Thermoplastic rubber (TPR) wheels
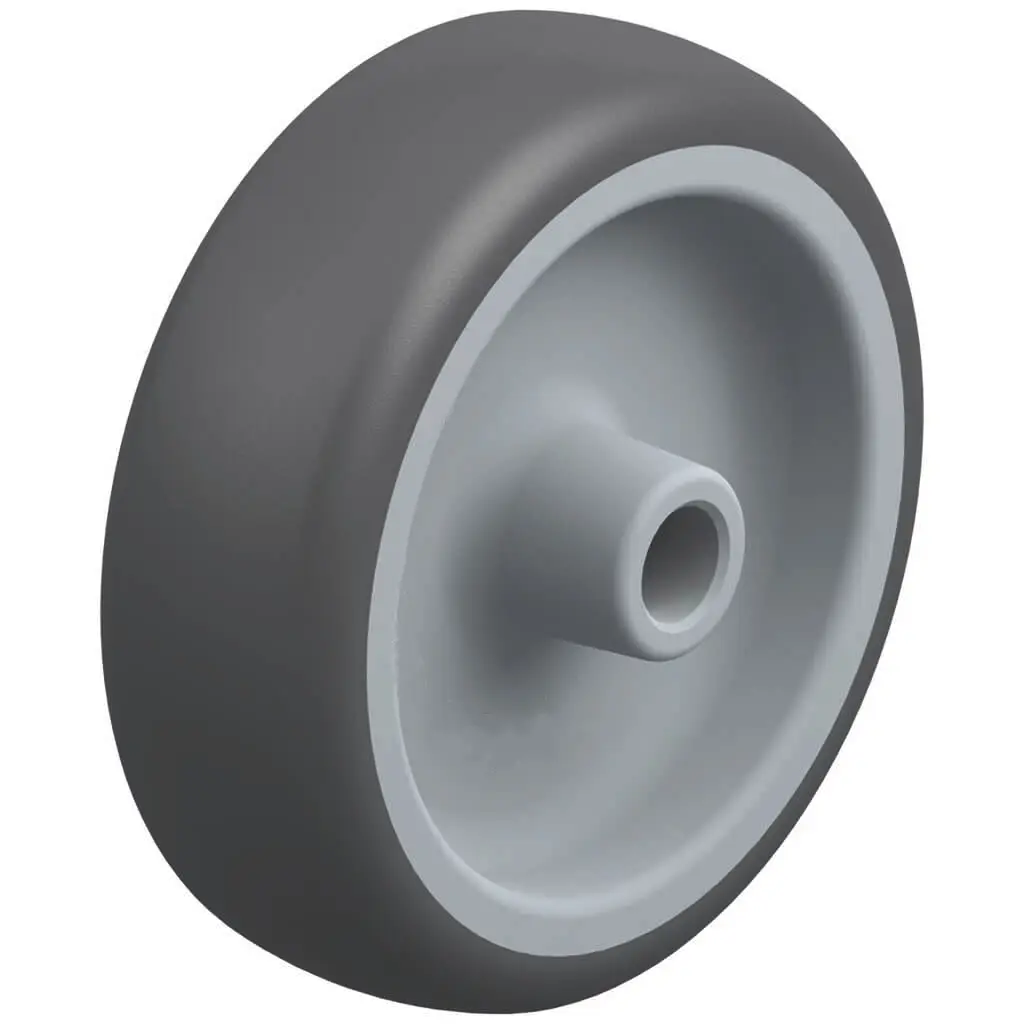
Characteristics:
Thermoplastic rubber (TPR) combines the flexibility of rubber with the durability of plastic, creating a versatile material that is commonly used in caster wheels. TPR wheels are known for their smooth operation and low rolling resistance.
Pros:
- Noise reduction: TPR wheels are quieter than harder materials, making them ideal for environments that require minimal noise, such as offices or hospitals.
- Smooth operation: Provides a smooth ride with less vibration, ensuring minimal disruption in operations.
- Good floor protection: Like rubber wheels, TPR offers excellent protection from scratches and damage for sensitive floors like hardwood, tiles, and linoleum.
- Good shock absorption: The cushioning effect of TPR helps minimize impact when transporting delicate items.
- Chemical resistance: Their resistance to various chemicals extends their usability in demanding environments.
- Economical: TPR casters are generally more cost-effective compared to other high-performance wheel options like polyurethane.
Cons:
- Lower load capacity: TPR casters typically have a lower load capacity compared to harder materials such as polyurethane or metal, making them less suitable for heavy-duty applications.
- Wear over time: They can wear out more quickly than other materials under continuous heavy use, leading to increased maintenance costs and more frequent replacements.
- Potential for flat spots: Under heavy loads or prolonged stationary periods, TPR wheels can develop flat spots that affect their performance.
- Sensitivity to sharp objects: TPR wheels may be prone to gouging or chunking when encountering sharp debris or rough surfaces.
Best Uses:
TPR caster wheels are commonly used in environments where noise reduction and smooth operation are priorities, such as in medical equipment, office furniture, shopping carts, janitorial equipment, warehouse applications, food service industry, laboratories, and event equipment.
Thermoplastic elastomer (TPE) wheels
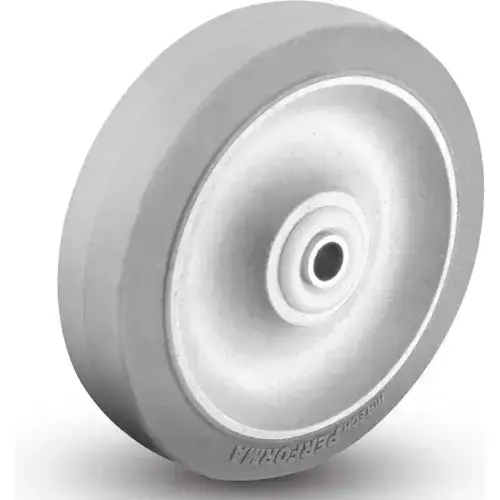
Characteristics:
Thermoplastic elastomer (TPE) caster wheels combine the properties of both rubber and plastic, making them highly flexible yet durable. They offer many similar benefits to TPR but tend to perform better under heavier loads.
Pros:
- Versatility: TPE wheels provide good performance on various surfaces, offering a balance between flexibility and durability.
- Chemical resistance: TPE wheels are resistant to oils, water, and other harsh chemicals.
- Good floor protection: Like rubber wheels, TPE offers excellent protection from scratches and damage for sensitive floors like hardwood, tiles, and linoleum.
- Good shock absorption: The cushioning effect of TPE helps minimize impact when transporting delicate items.
- Comparison with TPR: TPE wheels generally handle heavier loads more effectively than TPR wheels.
Cons:
- Lower load capacity: TPE casters typically have a lower load capacity compared to harder materials such as polyurethane or metal, making them less suitable for heavy-duty applications.
- Wear over time: They can wear out more quickly than other materials under continuous heavy use, leading to increased maintenance costs and more frequent replacements.
- Potential for flat spots: Under heavy loads or prolonged stationary periods, TPE wheels can develop flat spots that affect their performance.
- Sensitivity to sharp objects: TPE wheels may be prone to gouging or chunking when encountering sharp debris or rough surfaces.
Best Uses:
TPE caster wheels are commonly used in environments where noise reduction and smooth operation are priorities, such as in medical equipment, office furniture, shopping carts, janitorial equipment, warehouse applications, food service industry, laboratories, and event equipment.
Rubber on Aluminum core wheels
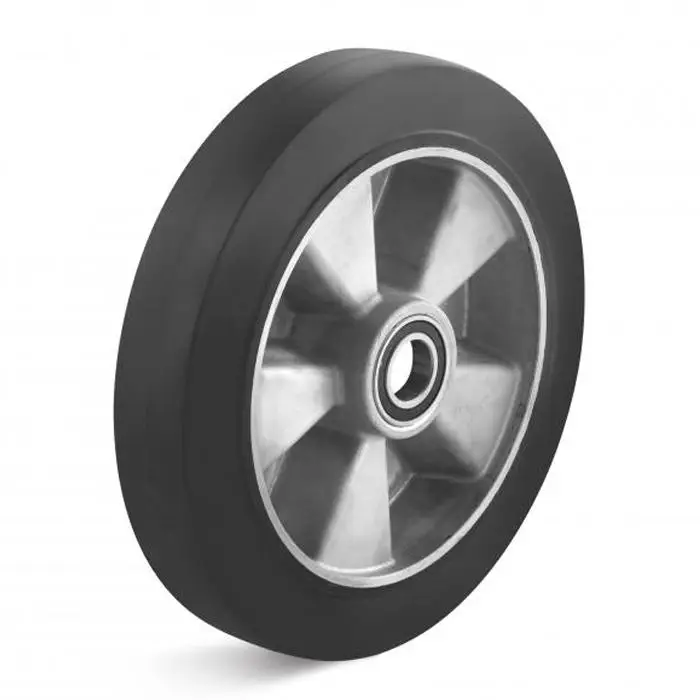
Characteristics:
Rubber on aluminum caster wheels combine the durability of rubber with the strength and lightweight properties of aluminum. This combination allows for a smooth, quieter ride with adequate load-bearing capability.
Pros:
- Lightweight: The aluminum core significantly reduces the overall weight of the wheel, making it easier to maneuver loads.
- Shock absorption: The rubber tread provides excellent shock absorption, which helps in protecting both the wheel and the surface being traversed from damage.
- Floor protection: Rubber wheels are gentle on floors, minimizing the risk of scratches or marks, making them suitable for use on sensitive surfaces like hardwood or tile.
- Good traction: Rubber offers superior grip on various surfaces, enhancing control during movement.
- Chemical resistance: These wheels resist many chemicals, oils, and cleaning agents, allowing for use in diverse environments without degradation.
- Quiet operation: The elasticity of rubber helps absorb vibrations and noise, making these wheels ideal for quiet environments such as offices and hospitals.
Cons:
- Limited Load Capacity: Rubber on aluminum wheels typically have a lower weight capacity compared to steel or polyurethane wheels, which may restrict their use in heavy-duty applications.
- Wear and Tear: Over time, the rubber can wear down more quickly than harder materials. Extended use under heavy loads can lead to flat spots or degradation of the tread.
- Sensitivity to Temperature: Rubber can be affected by extreme temperatures, potentially leading to reduced performance in very hot or cold conditions
Best uses:
These wheels are used in environments where smooth operation, versatility, and load-bearing capacity are needed, such as machinery, heavy-duty carts, and heavy-duty equipment.
(Mold on) Rubber on Cast Iron wheels
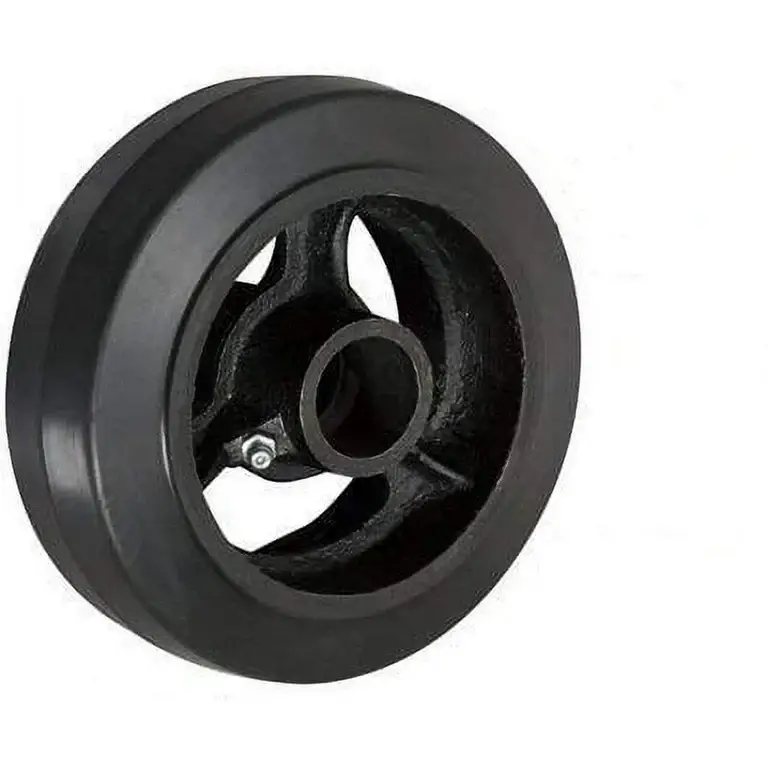
Characteristics:
Mold-on rubber on cast iron caster wheels combine the hardness of cast iron with the shock-absorbing and noise-reducing properties of rubber.
Pros:
- Material composition: These wheels feature a rubber tread that is bonded to a cast iron core, providing a sturdy yet cushioned option for various applications.
- High lcoad capacity: The cast iron core allows these wheels to support heavy loads, making them suitable for industrial and commercial environments where strength is required.
- Shock absorption: The rubber tread effectively absorbs shocks and vibrations, which helps protect both the items being transported and the surfaces they roll over.
- Durability: The combination of rubber and cast iron offers a durable solution that can withstand rough handling and challenging environments.
Cons:
- Weight: While durable, the cast iron core can make these wheels heavier than alternatives like aluminum or plastic, which may affect maneuverability.
- Wear over time: The rubber tread may wear down faster than harder materials under continuous heavy use or on rough surfaces, leading to potential replacements.
- Potential for flat spots: If left stationary under heavy loads for extended periods, these wheels can develop flat spots that hinder mobility.
- Sensitivity to chemicals: The rubber may be susceptible to degradation from certain chemicals or oils, limiting their use in specific industrial environments.
Best uses:
These wheels are perfect for heavy-duty applications like industrial carts, machinery, and scaffolding, where cost-effectiveness and durability are key priorities.
Polyurethane(PU) wheels
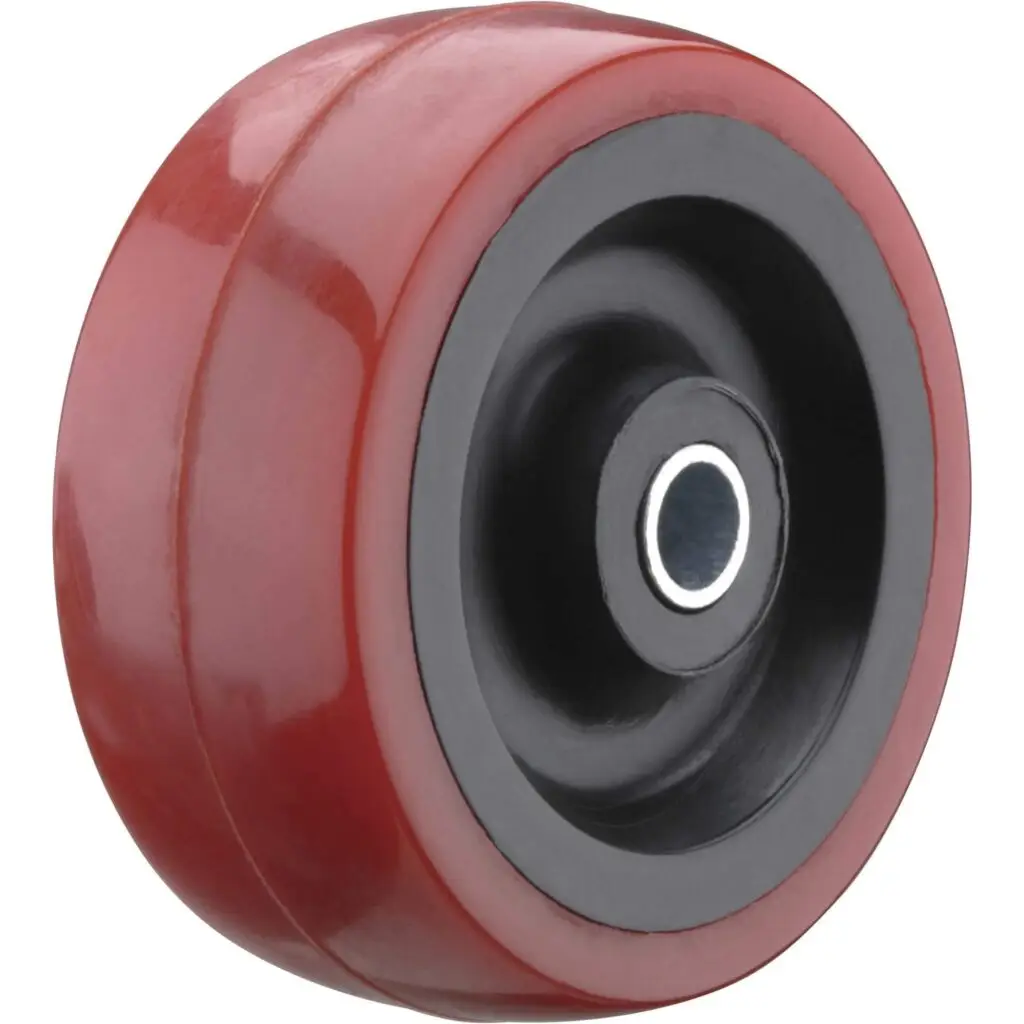
Characteristics:
Polyurethane (PU) caster wheels are made from a synthetic material that combines the flexibility of rubber with the durability of plastic. Polyurethane offers better resistance to wear and tear compared to rubber.
Pros:
- Durability: PU wheels typically last longer than rubber or plastic alternatives due to their superior material properties, often lasting up to three times longer than rubber
- High load capacity: They can handle more weight than standard rubber wheels, making them suitable for heavy-duty tasks
- Excellent shock absorption: The cushioning effect of PU provides protection for both the transported items and the surfaces they roll on.
- Non-marking properties: They protect floors from scratches and scuffs, maintaining the aesthetic integrity of sensitive surfaces.
- Resistance to chemicals: Many PU wheels can withstand exposure to various chemicals without degrading, making them versatile for different environments.
Cons:
- Higher cost: PU caster wheels generally come with a higher price tag compared to rubber wheels, which may be a consideration for budget-conscious buyers
- Potential for flat spots: While less prone than rubber wheels, PU wheels can still develop flat spots if left stationary under heavy loads for extended periods
- Sensitivity to high heat: PU can degrade at elevated temperatures; they typically tolerate ambient heat up to about 230°F but may melt under extreme conditions.
- Manufacturing defects: Defects can occur at the bond between the polyurethane tread and the wheel core, which may not be visible but can affect performance
- Will be hydrolyzed. What is Hydrolysis?
Best uses:
Polyurethane caster wheels are ideal for industrial environments, including warehouses, hospitals, and office equipment, where a balance of durability and floor protection is crucial.
Polyurethane(PU) on Aluminum wheels
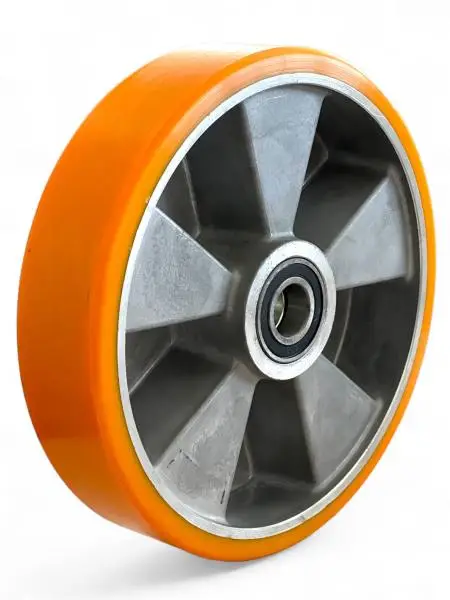
Characteristics:
Polyurethane on aluminum caster wheels combine the strength of aluminum with the flexibility and abrasion resistance of polyurethane, resulting in wheels that are both durable and able to handle a variety of surfaces.
Pros:
- High strength-to-weight ratio: Aluminum provides a lightweight yet strong base, while the polyurethane coating protects floors and enhances rolling resistance.
- Material composition: These wheels feature a high-quality liquid cast polyurethane tread that is chemically bonded to a solid aluminum core, providing a strong and lightweight option for various applications.
- Floor protection: The polyurethane material helps to prevent damage to floors.
- Material composition: These wheels feature a high-quality liquid cast polyurethane tread that is chemically bonded to a solid aluminum core, providing a strong and lightweight option for various applications.
- Non-marking: PU wheels are non-marking, preventing scuff marks on floors, which is essential in environments where aesthetics are important, such as hospitals and retail spaces.
- Durability: The combination of PU and aluminum results in a durable wheel that can withstand wear and tear, making it ideal for industrial environments.
- Chemical and Abrasion Resistance: These wheels exhibit excellent resistance to chemicals, oils, and solvents, as well as high abrasion resistance, allowing them to perform well in various settings.
Cons:
- Higher cost: PU on aluminum caster wheels tend to be more expensive than traditional rubber wheels, which may be a consideration for budget-conscious buyers.
- May not be as shock-resistant as some rubber or pneumatic wheels.
- Sensitivity to high heat: While generally heat-resistant, PU can degrade at elevated temperatures above 180°F; prolonged exposure may affect performance.
- Will be hydrolyzed: The PU will be hydrolyzed.
- Potential for flat spots: If left stationary under heavy loads for extended periods, these wheels can develop flat spots that affect mobility.
- Manufacturing defects: Defects at the bond between the polyurethane tread and the aluminum core may not be visible but can impact performance; choosing reputable manufacturers is crucial.
Best uses:
Polyurethane on aluminum caster wheels are ideal for industrial equipment, warehouse carts, and machinery, where strength, floor protection, and load-bearing capacity are essential.
Polyamide(Nylon) wheels
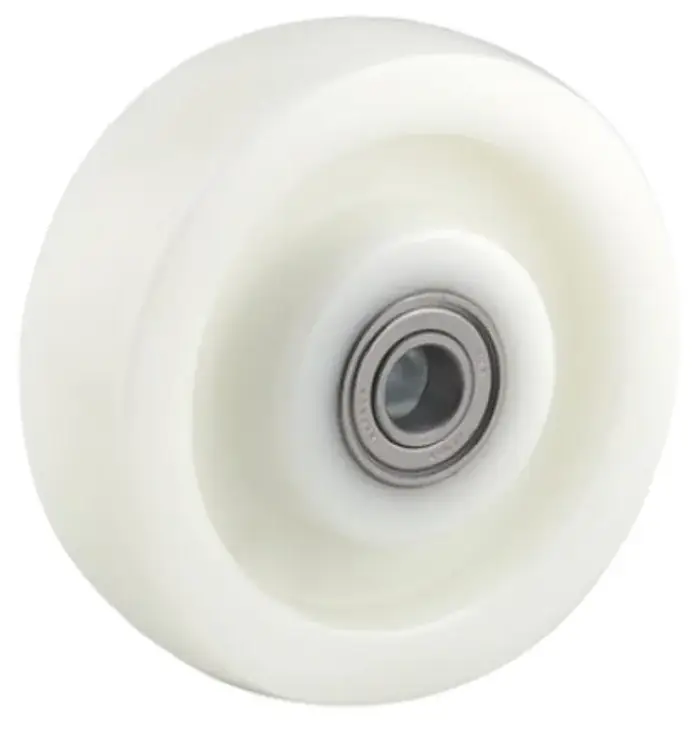
Characteristics:
Nylon is a hard, rigid material that offers excellent chemical resistance and resilience. It is lightweight and has a higher rolling resistance compared to softer materials like rubber and polyurethane.
Pros:
- Material composition: Made from synthetic nylon, these wheels are known for their toughness and resilience, suitable for heavy-duty applications.
- High load capacity: Nylon wheels can support significant weights without deforming, making them ideal for industrial settings where weight-bearing is critical.
- Wear resistance: Nylon has excellent abrasion resistance, which contributes to a longer lifespan even with frequent use, reducing maintenance costs and downtime.
- Low rolling resistance: The smooth surface of nylon minimizes friction, ensuring easy movement and reducing the effort needed to push or pull loads.
- Chemical resistance: Nylon is resistant to many chemicals, oils, and solvents, making these wheels suitable for environments where exposure to such substances is common.
- Temperature resilience: Nylon wheels can operate in a wide temperature range (typically from -30°C to +80°C), maintaining their integrity and performance in both cold and hot conditions.
- Non-marking: These wheels do not leave marks on floors, which is essential in settings where aesthetics are important.
Cons:
- Hardness may cause floordamage: The hardness of nylon can potentially damage sensitive flooring surfaces like hardwood or tiles if floor protection is a priority.
- Noisy operation: Nylon wheels tend to generate more noise during operation compared to softer materials like rubber or polyurethane, which can be a disadvantage in noise-sensitive environments.
- Static electricity generation: Nylon can generate static electricity, which might be an issue in environments sensitive to static discharge. Antistatic options may be necessary in such cases.
- Higher cost compared to some materials: While they offer durability, nylon caster wheels can be more expensive than options like rubber or plastic; however, their longevity may offset this initial cost.
Best uses:
Nylon caster wheels are typically used in chemical processing industries, clean rooms, and warehouses, where resistance to chemicals and heavy load capacity are prioritized.
Polypropylene(PP) wheels
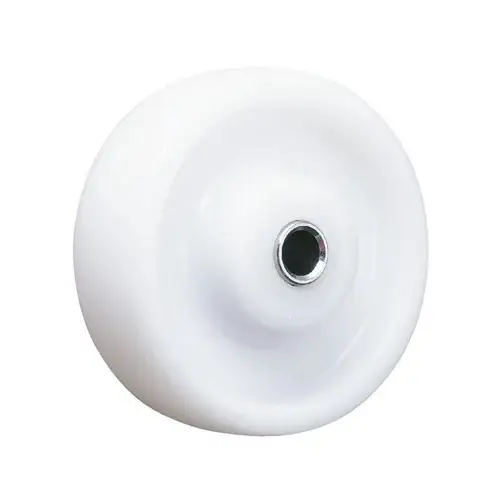
Characteristics:
Polypropylene is a thermoplastic that is lightweight and resistant to chemical damage. These wheels can be made in both standard and V-grooved types.
Pros:
- Cost-effective: PP caster wheels are generally more affordable than other options, making them an economical choice for budget-conscious applications.
- Lightweight: PP wheels are significantly lighter than many other materials, making them easy to handle and maneuver.
- Chemical resistance: They exhibit excellent resistance to a wide range of chemicals, oils, and solvents, which makes them suitable for various environments, including those involving cleaning agents.
- Non-marking: These wheels are designed to be non-marking, preventing scuffs and scratches on floors, which is crucial in settings like retail and healthcare.
- Moderate load capacity: While they can handle light to medium loads effectively, PP wheels generally have a lower load capacity compared to heavier-duty materials like nylon or polyurethane.
Cons:
- Lower load capacity: These wheels are not suitable for heavy-duty applications as they can deform under excessive weight, limiting their use in industrial settings.
- Durability on rough surfaces: While effective on smooth surfaces, PP wheels may wear out quickly on rough or abrasive floors, leading to a shorter lifespan in such conditions.
- Limited shock absorption: Compared to softer materials like rubber or polyurethane, PP wheels offer less cushioning and shock absorption, which may not be ideal for transporting sensitive items.
- Noise level: They can be noisier during operation compared to softer wheel materials, which could be a concern in noise-sensitive environments.
Best uses:
Polypropylene wheels are commonly used in food processing plants, clean rooms, and light industrial applications where cost-effectiveness and chemical resistance are the primary concerns.
Cast Iron wheels
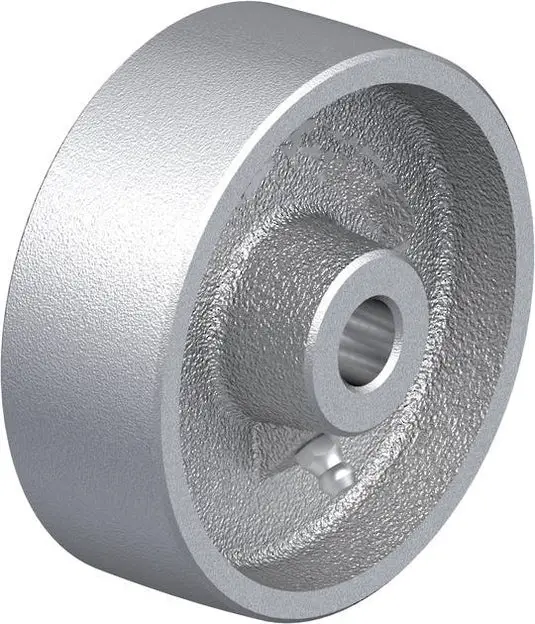
Characteristics:
Cast iron wheels are extremely durable and capable of handling extremely heavy loads. They are made from molten iron poured into molds, offering both strength and longevity.
Pros:
- High load capacity: Cast iron wheels can support substantial weights, often exceeding 1,000 lbs, making them ideal for heavy-duty applications.
- Temperature resistance: Cast iron can endure high temperatures, making it suitable for environments like bakeries or manufacturing processes that involve heat.
- Long lifespan: Due to their durability, cast iron wheels tend to have a long service life, especially in static applications where they bear heavy loads without movement.
Cons:
- Noise levels: Cast iron wheels can be noisy when rolling, which may not be suitable for environments where noise reduction is essential.
- Floor damage: Their hardness can lead to potential damage on sensitive flooring surfaces like hardwood or tiles, especially if the load is heavy or if the wheels are not designed with protective features.
- Weight: While their weight contributes to stability, it can make them more challenging to maneuver compared to lighter materials like rubber or nylon.
Best uses:
These wheels are best suited for heavy machinery in industrial settings, such as in factories, warehouses, and automotive applications.
Forged Steel wheels
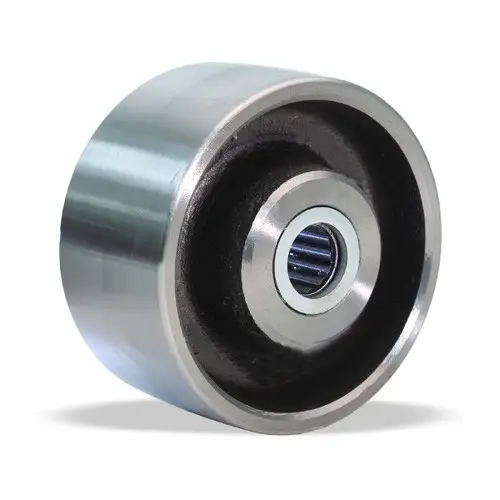
Characteristics:
Forged steel caster wheels are manufactured from high-grade steel, offering immense strength and high load-bearing capacity. These wheels are typically used in environments that require both strength and high-temperature resistance.
Pros:
- High load capacity: Forged steel wheels can support significant weights, often exceeding 5,000 lbs, making them ideal for heavy machinery and equipment.
- Impact resistance: The forging process gives these wheels superior impact strength, allowing them to absorb shocks and withstand severe conditions without deforming.
- Wear resistance: Forged steel offers excellent resistance to wear and tear, ensuring a longer lifespan even in demanding environments.
- Heat resistance: These wheels can operate effectively in high-temperature conditions, withstanding temperatures up to 800°F with appropriate bearings and lubrication.
- Cost-effective long-term: Although initially more expensive than other wheel types, their durability reduces the need for frequent replacements, leading to lower maintenance costs over time.
Cons:
- Higher initial cost: Forged steel wheels typically have a higher upfront cost due to the intensive manufacturing process involved in forging.
- More expensive: Compared to other materials.
- Weight: They are heavier than alternatives like rubber or nylon wheels, which may complicate movement in some applications where weight is a concern.
- Noise levels: Forged steel wheels can be noisier during operation compared to softer materials, which may not be suitable for noise-sensitive environments like hospitals or offices.
Best uses:
Forged steel caster wheels are typically used in high-load environments such as steel mills, foundries, and automotive industries, where heavy-duty performance and heat resistance are critical.
Phenolic / High temp resist wheels
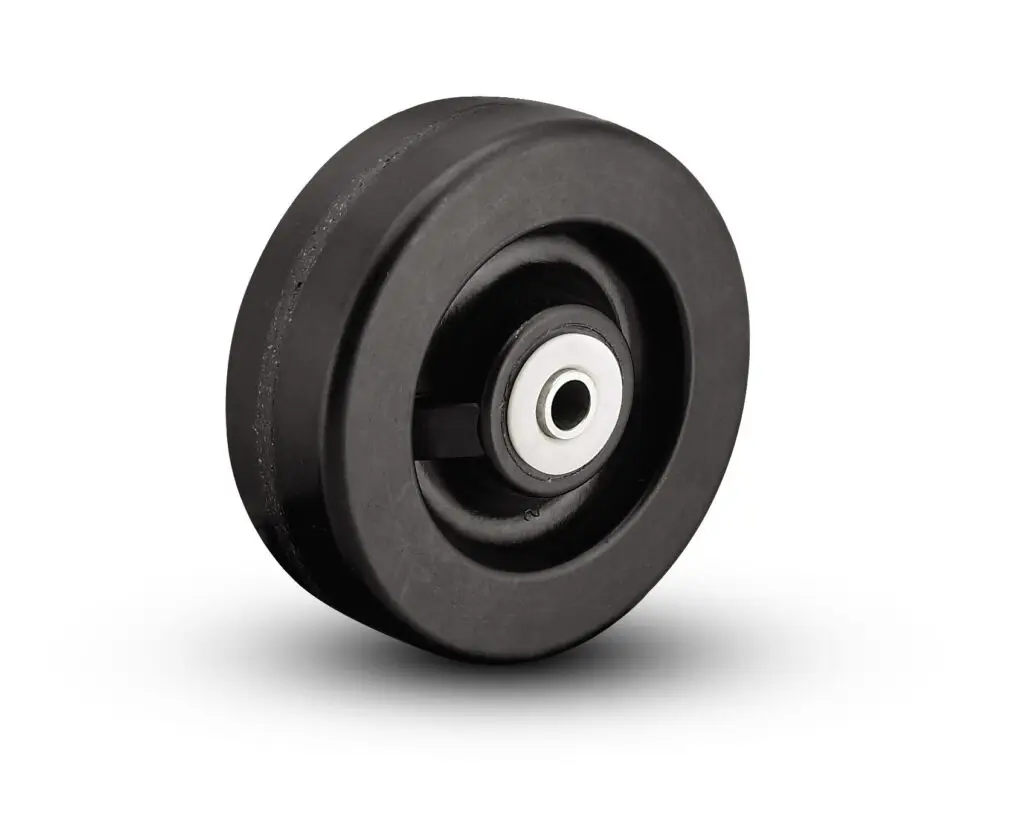
Characteristics:
Phenolic caster wheels are made from a thermoset plastic that is reinforced with fiberglass, providing high durability and strength.
Pros:
- Material Composition: Made from phenolic resin, often reinforced with materials like cotton or linen, these wheels are designed to withstand significant wear and tear.
- Durability: The strong construction allows phenolic wheels to withstand heavy loads and rough handling, making them ideal for industrial applications.
- Heat and Chemical Resistance: Their ability to resist high temperatures of 250℃ (500℉)and various chemicals makes them versatile for different industrial settings.
- High load support: Can support heavy loads and are capable of performing in environments with moderate temperatures.
- Cost-effective: Low maintenance compared to metal wheels.
Cons:
- Debris retention: Phenolic wheels can pick up debris, which may lead to increased noise and difficulty in movement over time.
- Limited shock absorption: They offer less cushioning compared to softer wheel materials, which may impract load stability on uneven surfaces.
- Moisture absorption risk: If the outer shell is compromised (e.g., chipped), phenolic wheels can absorb moisture, leading to potential degradation and reduced performance.
Best uses:
These wheels are often used in industrial applications, such as warehouses, factories, and material handling equipment, where strength and durability are required but shock absorption is not the primary concern.
Pneumatic wheels
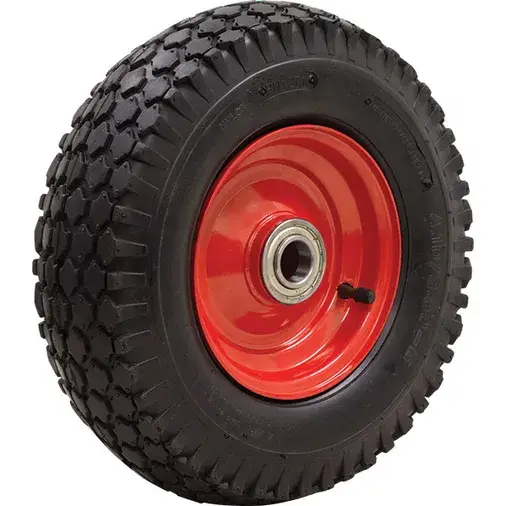
Characteristics:
Pneumatic caster wheels are air-filled wheels that offer excellent shock absorption and are ideal for rough or uneven surfaces.
Pros:
- Excellent shock absorption: Reduce impact by up to 40%, making them ideal for outdoor or rugged terrain applications.
- Smooth ride: Pneumatic casters offer a smoother ride over rough or uneven surfaces, reducing operator fatigue and improving comfort.
- Good traction: Pneumatic wheels provide better grip on various surfaces, reducing slippage and enhancing stability during movement.
- Floor protection: Their softer material minimizes the risk of damaging floors, making them suitable for use in environments with sensitive flooring.
Cons:
- Susceptible to punctures: Like any air-filled tire, pneumatic casters can be punctured by sharp objects, leading to deflation and requiring maintenance.
- Less ideal for smooth surfaces: Due to their rolling resistance, pneumatic wheels are not suitable for smooth surfaces like tiles or hardwood.
- Increased push force required: Moving heavy loads on pneumatic casters may require more effort compared to solid wheels due to their design.
- Limited load capacity: While they can handle moderate loads, pneumatic casters generally have a lower load capacity compared to solid or heavy-duty wheels.
Best uses:
Pneumatic caster wheels are widely used in outdoor applications, such as for construction equipment, garden carts, and off-road vehicles, where shock absorption is needed on rough terrains.
Foam rubber wheels
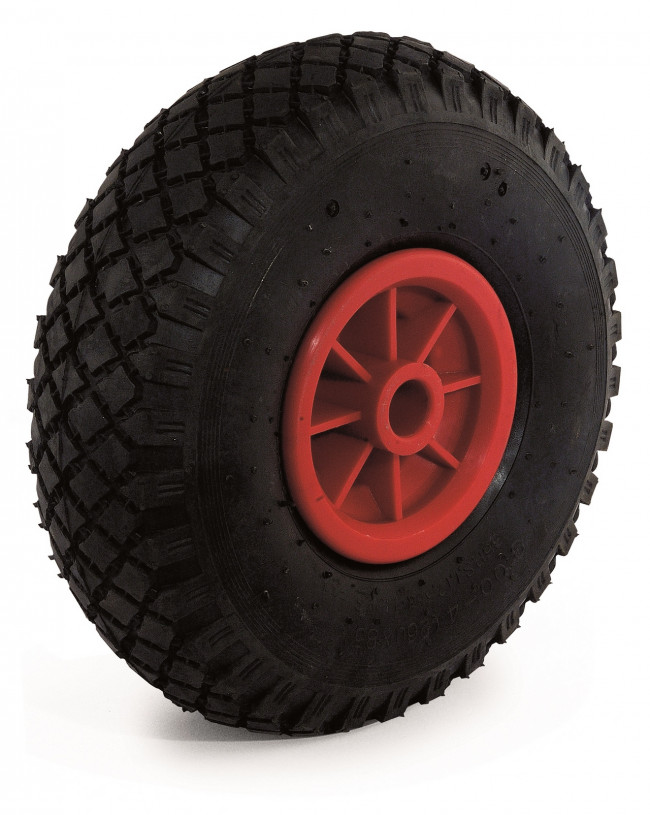
Characteristics:
Foam rubber caster wheels are constructed by filling pneumatic tires with a polyurethane foam that solidifies, eliminating the air inside and making them flat-proof. This innovative design enhances durability by making the wheels resistant to punctures, ideal for environments with sharp debris.
Pros:
- Flat-Proof: The primary advantage is that they cannot go flat, making them ideal for use in construction or industrial environments where punctures are common.
- Low Maintenance: They require minimal maintenance compared to pneumatic tires since there is no need for regular pressure checks.
- Stability: The added weight can enhance stability during operation, particularly in rough terrains.
- Durability: Foam rubber wheels have a longer lifespan than traditional pneumatic tires due to their resistance to punctures and wear
- Consistent Performance: They maintain a consistent performance throughout their lifespan since they do not lose air pressure.
Cons:
- Ride Comfort: They generally offer a harsher ride compared to pneumatic tires due to the absence of air cushioning, which can lead to discomfort on uneven surfaces
- Weight Issues: Their heavier weight can make them harder to push and maneuver, affecting overall efficiency
- Cost: While they may save money on maintenance, foam-filled tires can be more expensive upfront compared to traditional pneumatic tires
- Less Traction: The smaller footprint can result in reduced traction, which may impact performance in certain applications
- Limited Sidewall Protection: Foam rubber wheels may have less sidewall protection compared to solid rubber tires, leading to potential failures if not used correctly
Best uses:
asfdasfasfsaf
Conductive and Anti-Static wheels
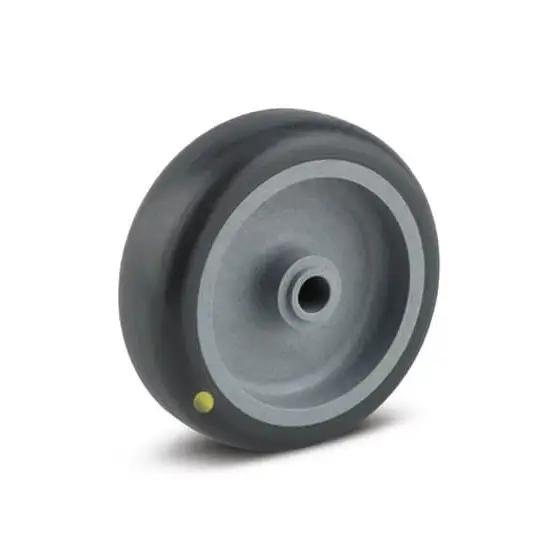
Characteristics:
Conductive and anti-static caster wheels are designed to dissipate static electricity, making them ideal for use in environments where sensitive electronic equipment is at risk.
Pros:
- Static control: Both types effectively manage static electricity, protecting sensitive electronic devices and preventing electrostatic discharge that could harm equipment or cause explosions in hazardous environments
- Durable and safe: These wheels are made from materials that are both durable and capable of providing a safer environment for electronics.
- Non-marking: Most conductive wheels are also non-marking, ensuring floors remain pristine.
Cons:
- Cost: Conductive and anti-static caster wheels can be more expensive than standard wheels due to their specialized materials and manufacturing processes
- Limited floor compatibility: These wheels work best on specific surfaces like concrete or anti-static flooring.
Best uses:
These caster wheels are commonly used in industries that handle electronics, computer equipment, or semiconductors, where protection from static electricity is critical.
Factors to Consider When Choosing Caster Wheel Materials
Choosing the right caster wheel material involves more than just the type of floor and load requirements; it also takes into account several important factors. Below are key considerations to ensure you select the right material for your needs.
Load Capacity
The material of the caster wheel affects how much weight it can handle. For example, polyurethane and forged steel offer high load-bearing capacity, while rubber and TPE are more suited for lighter loads.
When choosing a caster wheel, assess the weight of the equipment or object that will be moved. Be sure to select a material that can comfortably bear the load while maintaining smooth and efficient movement.
Floor Types and Compatibility
Different caster materials perform better on different surfaces. Rubber and TPR wheels are perfect for protecting sensitive floors like wood or tile, while steel and cast iron may cause damage if used on these surfaces.
Consider your floor type—whether it’s concrete, carpet, or tile—and select a material that provides the best performance without compromising the floor’s integrity.
Environmental Conditions
The temperature, humidity, and exposure to chemicals in your environment can significantly affect the performance of caster wheels. For instance, nylon and polyurethane work well in harsh environments, while rubber wheels may degrade under UV exposure or in high temperatures.
When choosing caster wheels, make sure to account for environmental conditions, such as temperature extremes and chemical exposure, to ensure the wheels maintain their functionality over time.
Durability and Maintenance
Caster wheel durability depends on the material and its ability to resist wear. For example, polyurethane wheels last longer than rubber wheels, especially in industrial environments, where they can last up to 3 times longer than rubber.
Additionally, consider the maintenance required for the wheels. Some materials like TPR require less maintenance, while others like steel or cast iron may need regular cleaning to avoid damage.
Environmental Impact and Sustainability
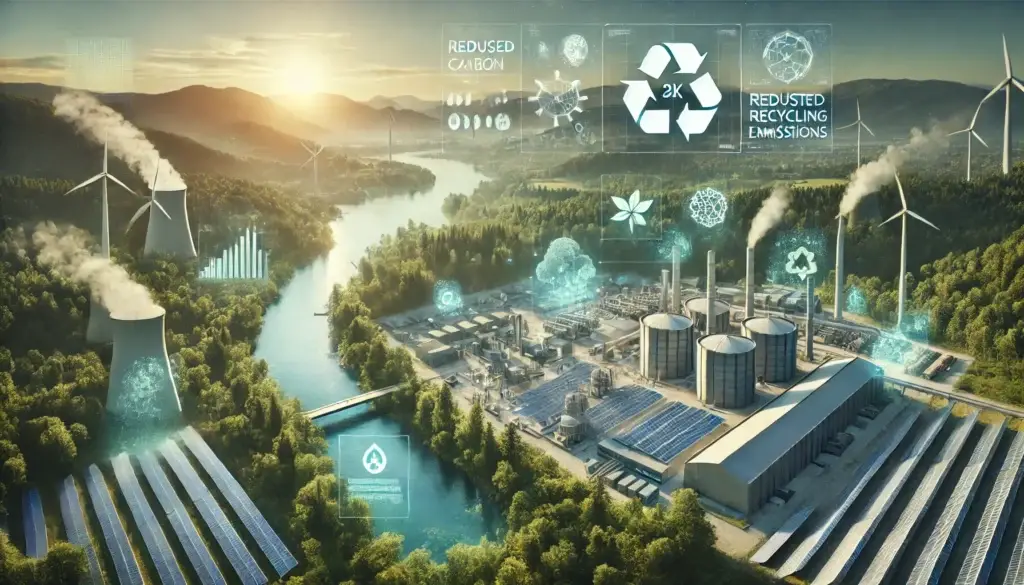
The choice of caster wheel material is not only about performance but also about sustainability and environmental impact. As businesses and industries increasingly focus on reducing their carbon footprint, choosing eco-friendly caster wheel materials becomes a priority.
Material Sustainability
Some materials, such as rubber and polyurethane, can have a significant environmental impact due to their manufacturing processes and disposal concerns. Rubber, especially, is derived from natural rubber or synthetic rubber, both of which have ecological implications in their production and disposal. Polyurethane, while durable, is not biodegradable and can contribute to plastic waste in the long term.
On the other hand, materials like TPE (thermoplastic elastomer) and TPR (thermoplastic rubber) are made using more sustainable processes. These materials can be recycled, which reduces waste and their environmental footprint. Additionally, polyurethane on aluminum caster wheels offer a combination of metal and plastic, making them a good option for strength and floor protection while allowing for easier recycling of components.
Reducing Environmental Footprint
The global market for eco-friendly caster wheels is expected to grow by 7% annually through 2030. This growth is driven by the increasing demand for products that reduce environmental harm. Companies can contribute to sustainability by opting for recyclable materials, choosing longer-lasting wheels that require less frequent replacement, and selecting manufacturers that prioritize environmentally responsible production methods.
Waste Reduction Strategies
To minimize waste, it’s essential to choose caster wheels that offer a longer lifespan. For example, polyurethane wheels last significantly longer than rubber wheels in industrial environments, reducing the need for frequent replacements. Additionally, when the wheels reach the end of their lifespan, opting for recyclable polyurethane on aluminum wheels or TPE caster wheels helps reduce landfill waste.
Incorporating these sustainable practices into material selection not only helps businesses become more environmentally responsible but also aligns with global initiatives aimed at reducing waste and promoting eco-friendly manufacturing.
Case Studies and Real-World Applications
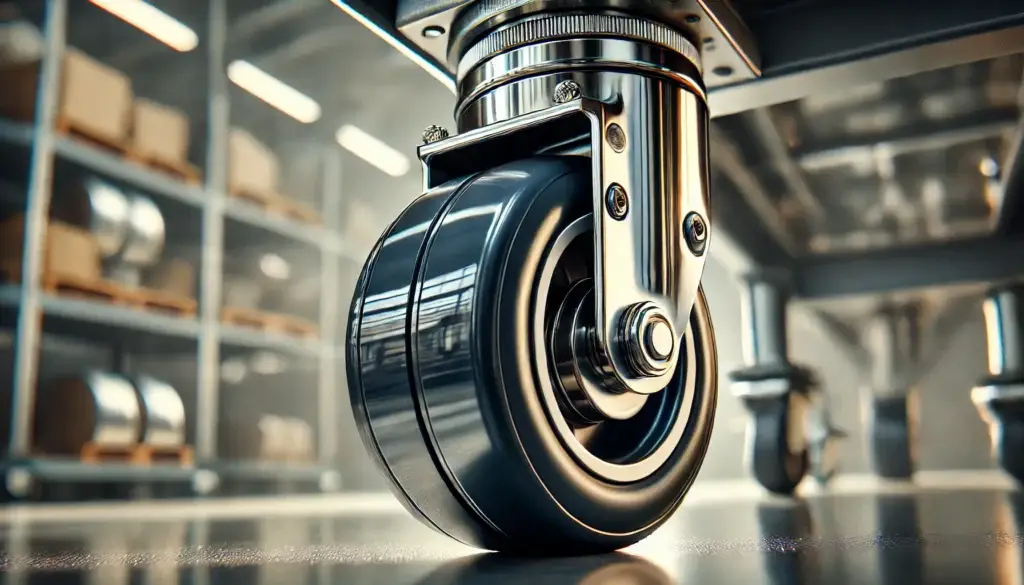
Case Study 1: Manufacturing Plant Optimization
A large automotive manufacturing plant sought to improve the mobility and efficiency of their heavy machinery. They transitioned from cast iron caster wheels to polyurethane wheels.
Challenge: Cast iron wheels were causing significant floor damage and contributing to noise pollution, affecting both equipment longevity and worker comfort.
Solution: Switching to polyurethane caster wheels provided a smoother ride, reduced noise levels, and minimized floor wear.
Outcome: The plant experienced a 30% reduction in maintenance costs, extended equipment lifespan, and improved worker satisfaction due to the quieter environment.
Case Study 2: Retail Display Enhancement
A prominent retail chain wanted to enhance the mobility of their product displays without compromising the aesthetic appeal or damaging delicate flooring.
Challenge: Existing nylon caster wheels were not providing adequate floor protection and were prone to slipping on polished surfaces.
Solution: Upgrading to rubber caster wheels ensured floor protection and provided a non-slip surface, enhancing the overall presentation of the displays.
Outcome: The retailer reported a significant decrease in floor damage, improved display mobility, and received positive feedback from store managers regarding the enhanced aesthetics.
Case Study 3: Medical Equipment Mobility
A hospital needed to improve the mobility of their medical equipment, such as hospital beds and infusion pumps, ensuring both durability and floor protection.
Challenge: Polyolefin wheels previously used were not providing sufficient floor protection and were causing scratches on sensitive surfaces.
Solution: Transitioning to polyurethane caster wheels offered superior floor protection, silent operation, and high durability, essential for a busy medical environment.
Outcome: The hospital experienced reduced maintenance issues, enhanced equipment mobility, and improved patient comfort due to the quieter wheels.
Case Study 4: Construction Equipment Durability
A construction company required caster wheels for their heavy-duty equipment operating on rough terrain and uneven surfaces.
Challenge: Nylon caster wheels were insufficient for the rough terrain, leading to frequent wheel damage and inefficient movement of equipment.
Solution: Implementing pneumatic caster wheels provided the necessary shock absorption and mobility over uneven surfaces, enhancing operational efficiency.
Outcome: The company reported a 50% increase in equipment mobility, reduced wheel damage, and enhanced overall productivity on construction sites.
Case Study 5: Office Furniture Upgrade
An office building aimed to upgrade their office furniture, including chairs and cabinets, to improve mobility and floor protection.
Challenge: Rubber caster wheels were causing noise and were not aesthetically aligned with the office’s modern design.
Solution: Switching to polyurethane caster wheels provided a quiet operation, better floor protection, and a sleek appearance that matched the office decor.
Outcome: The office enjoyed a quieter workspace, reduced floor maintenance costs, and enhanced aesthetic appeal of their furniture.
Technological Innovations
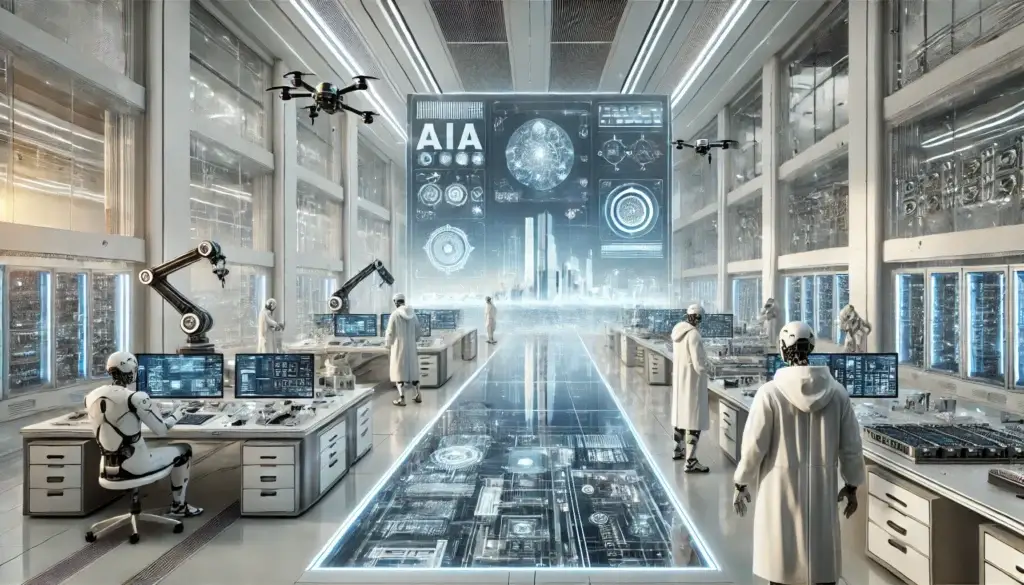
The global caster wheels market is expected to grow at a compound annual growth rate (CAGR) of 6% from 2023 to 2029. This growth is driven by the increasing adoption of industrial automation. As industries evolve, new advancements in caster wheel technology are emerging to meet diverse and changing needs. Innovations like smart caster wheels and eco-friendly materials point to a promising future for the industry by providing better performance and sustainability. Although some of these technologies are still being developed, they have the potential to significantly change how caster wheels are used in different applications.
Smart Caster Wheels
Integrated Sensors:
Incorporation of sensors into caster wheels to monitor performance, load capacity, and wear in real-time, enabling predictive maintenance.
IoT Connectivity:
Linking caster wheels to Internet of Things (IoT) platforms for remote monitoring and data analysis, enhancing operational efficiency and equipment management.
Emerging Materials
Advanced Polymers:
Development of high-performance polymers that offer enhanced durability, flexibility, and chemical resistance.
Biodegradable Materials:
Research into biodegradable caster wheel materials to further reduce environmental impact and support sustainability initiatives.
3D Printing and Customization
Custom Designs:
Utilization of 3D printing technologies to create customized caster wheel designs tailored to specific applications and requirements.
Rapid Prototyping:
Accelerating the development process by enabling rapid prototyping of new caster wheel models and materials.
Sustainable Manufacturing Practices
Energy-Efficient Production:
Adoption of energy-efficient manufacturing processes to reduce the carbon footprint and resource consumption.
Recycling Programs:
Expansion of recycling programs to repurpose used caster wheels and minimize waste in the production cycle.
Conclusion
Selecting the right caster wheel material is critical to the performance, safety, and efficiency of your operations. Understanding the characteristics, pros, and cons of each material—whether it’s rubber, polyurethane, nylon, or steel—can help you make an informed decision based on your specific needs. Consider factors like load capacity, floor compatibility, environmental conditions, and maintenance requirements to ensure optimal wheel performance.
By carefully choosing the appropriate caster wheel material for your application, you’ll not only enhance operational efficiency but also contribute to a more sustainable future. Remember, the best choice will depend on your unique environment and the demands of your industry.
If you got questions or a unique application in mind, contact us or email us at eric@wheelswaycaster.com—we’re here to help!
FAQs
u003cstrongu003eQ: What caster wheel material is best for heavy-duty applications?u003c/strongu003e
A: Forged steel and cast iron caster wheels are the most suitable for heavy-duty applications due to their high load-bearing capacity and durability.
u003cstrongu003eQ: What is the difference between TPE and TPR caster wheels?u003c/strongu003e
A: TPE (Thermoplastic Elastomer) is essentially a softer and more flexible variant of TPR(Thermoplastic Rubber). TPE is chosen when greater flexibility and softness are desired.u003cbru003eOn the Shore durometer scale, TPE wheels typically have a hardness of 70–75 Shore A, whereas TPR wheels range from 85–90 Shore A.
u003cstrongu003eQ: Can conductive caster wheels prevent electrostatic discharge in electronics?u003c/strongu003e
A: Yes, electrically conductive caster wheels protect static-sensitive electronic equipment by directing static electricity to conductive flooring instead of the cart or the equipment itself.
u003cstrongu003eQ: What are the most common materials used for caster wheels?u003c/strongu003e
A: Rubber, TPR, TPE, PU, PP, and Nylon are the most common material used for caster wheels.