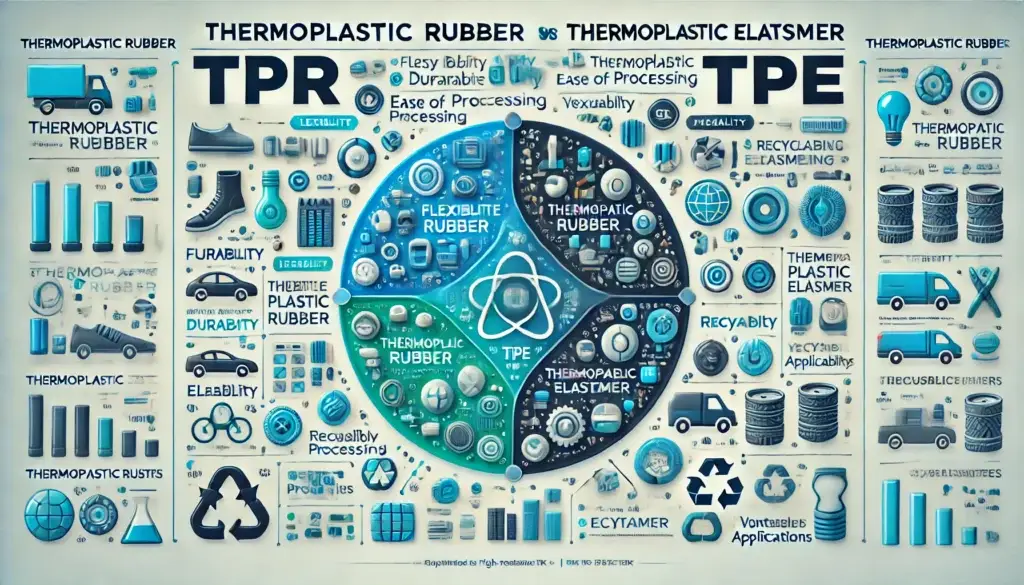
Similarities
When comparing Thermoplastic Rubber (TPR) and Thermoplastic Elastomer (TPE), it’s clear these materials share a wealth of similarities that have made them indispensable across various industries. Let’s break down their shared characteristics to see why they’re so widely used.
1. Thermoplastic nature
Both TPR and TPE fall under the thermoplastic category, meaning they have the ability to be melted, reshaped, and hardened without losing their structural integrity. This characteristic makes them highly reusable, as they can undergo repeated cycles of processing without significant degradation. Whether you’re designing a product for its first use or recycling an old one, these materials offer flexibility in application.
2. Elastic Nature
One standout feature of both materials is their rubber-like elasticity. They can stretch significantly under stress and then return to their original shape once the pressure is released. This combination of flexibility and resilience makes them ideal for applications such as seals, gaskets, and other components where durability and pliability are crucial.
3. Simple manufacturing
Another point of similarity is their compatibility with standard thermoplastic processing equipment. Techniques like injection molding, extrusion, and blow molding are commonly employed with both materials. This ease of production not only simplifies manufacturing processes but also reduces associated costs.
4. Versatility
One of the most valuable traits of TPR and TPE is their adaptability. They can be customized to meet specific performance criteria, ensuring that industries from automotive to healthcare can utilize them effectively. Their ability to be tailored means they are found in diverse settings, ranging from medical devices to consumer electronics.
5. Recyclable and Sustainable
The thermoplastic nature of both materials extends to their recyclability. They can be reprocessed after initial use, making them a more environmentally friendly option compared to thermoset rubbers, which cannot be remolded once cured. This property aligns well with growing sustainability goals in manufacturing.
6. High Fatigue Resistance
Fatigue strength, or the ability to withstand repeated stress without failure, is another area where TPR and TPE shine. Their resistance to tearing and abrasion makes them a go-to choice for products expected to endure rigorous conditions, such as conveyor belts or high-performance hoses.
7. Cost-Effectiveness
From a cost perspective, TPR and TPE strike a balance between affordability and performance. Manufacturers often favor these materials because they offer dependable quality while keeping production expenses in check. This cost-effectiveness helps businesses optimize budgets without compromising on product standards.
In essence, TPR and TPE have cemented their status as versatile, durable, and cost-efficient materials, making them an excellent choice for countless applications.
Differences Between TPR and TPE
Despite their numerous similarities, TPR and TPE also exhibit distinct characteristics that set them apart. These differences often influence the decision of which material to use for a given application.
TPR | TPE |
---|---|
Tensile strength ranges between 10 to 40 MPa | Tensile strength ranges between 5 to 20 MPa |
elongation at break ranging from 300% to 800% | elongation at break ranging from 150% to 600% |
Excellent chemical resistance | may not hold up as well against certain solvents |
Perform well from -50°C to +125°C | Perform well from -30°C and +70°C |
Requires higher temperatures and more techniques to process | Lower processing demands |
May release harmful substances upon degradation | More environmentally friendly |
Glossy finish | Matte appearance |
good dynamic performance but may harden significantly at lower temperatures | Maintains consistent flexibility across its temperature range in frequent movement |
Cost-effective | Higher cost than TPR |
1. Physical Properties
When it comes to tensile strength and elasticity, TPR generally outperforms TPE. TPR’s tensile strength ranges between 10 to 40 MPa, making it suitable for demanding applications. It can also stretch significantly, with elongation at break ranging from 300% to 800%. In contrast, TPE offers more moderate tensile strength (5 to 20 MPa), with elongation at break ranging from 150% to 600%, but compensates with greater flexibility, particularly in applications requiring smooth movement.
2. Chemical Resistance
TPR excels in resisting oils and greases, making it a prime candidate for automotive and industrial uses. TPE, while also resistant to many chemicals, may not hold up as well against certain solvents. However, TPE often boasts a broader range of formulation options, making it adaptable to niche requirements without relying heavily on oil-based additives.
Chemicals | TPR | TPE |
---|---|---|
Oil and greases | Excellent | Excellent |
Alcohols | Excellent | Good |
Water | Excellent | Excellent |
Cleaning agent | Good | Good |
Detergents | Good | Good |
Aromatic hydrocarbons | Moderate | Good |
Halogenated hydrocarbons | Moderate | Moderate |
Dilute acids and Dilute Alkalis | Excellent | Excellent |
Aliphatic hydrocarbons | Excellent | Excellent |
3. Temperature Tolerance
TPR operates effectively across an impressive temperature range of -50°C to +125°C. This wide spectrum ensures performance in both extremely cold and hot conditions. TPE, on the other hand, performs best between -30°C and +70°C but retains its flexibility even at lower temperatures, giving it an edge in some colder environments.
4. Processing Requirements
While both materials are relatively easy to process, TPR often requires higher temperatures and more specialized techniques due to its rubber content. TPE, with its lower processing demands, integrates seamlessly with standard thermoplastic methods, making it more accessible for manufacturers.
5. Environmental Impact
TPE tends to be the more environmentally friendly option. Its superior recyclability and cleaner degradation process make it a better fit for sustainable production. Conversely, TPR may release harmful substances upon degradation, posing potential environmental risks.
6. Surface and Texture
The tactile differences between the two are subtle but impactful. TPR often features a glossy finish with a slightly viscous feel, particularly at moderate temperatures. TPE, by contrast, is known for its matte appearance and smooth texture, which enhances its appeal in consumer products like grips and handles.
7. Performance Under Dynamic Stress
Dynamic applications reveal another key difference: TPR may harden in cold conditions, affecting its flexibility. Meanwhile, TPE maintains consistent pliability across its temperature range, making it better suited for scenarios involving frequent movement.
8. Market Preferences and Costs
TPR tends to be a cost-effective option for applications that don’t demand peak performance, whereas TPE’s higher price tag is often justified by its superior properties. Industries requiring high-performance materials frequently lean toward TPE despite its slightly higher cost.
These nuanced differences highlight the unique strengths of each material, ensuring they cater to distinct industrial needs.
What is TPR?
Thermoplastic Rubber, commonly referred to as TPR, is an innovative material that blends the desirable traits of both rubber and plastic. It stands out for its unique combination of elasticity, durability, and ease of processing, making it a favorite across multiple industries.
At its core, TPR is a synthetic rubber material. It’s often modified from SBS (styrene-butadiene-styrene block copolymers), which is further enhanced with additives to improve their performance. This carefully engineered structure grants TPR the ability to mimic the flexibility and resilience of natural rubber while retaining the moldability of plastics.
What is TPE?
Thermoplastic Elastomer, or TPE, is a family of materials designed to combine the elastic properties of rubber with the processing benefits of plastics. It’s most commonly modified from SEBS (Styrene Ethylene Butylene Styrene Block Copolymer) base material. Unlike single-material solutions, TPE is often composed of a physical blend of polymers, making it exceptionally versatile and customizable.
TPEs can be categorized into various types based on their chemical composition. These include styrenic block copolymers (SBCs), thermoplastic polyurethanes (TPUs), and thermoplastic polyolefins (TPOs), among others. Each category offers unique characteristics tailored to specific applications. For instance, TPU is celebrated for its resistance to abrasion and chemicals, making it ideal for demanding industrial environments, while SBCs are often chosen for consumer products due to their soft texture and flexibility.
Rolling Performance on Various Floors
Floor surface | TPR | TPE |
---|---|---|
Concrete Floors | Excellent | Excellent |
Hardwood Floors | Excellent | Excellent |
Carpeted Surfaces | Moderate | Moderate |
Tile Floors | Excellent | Excellent |
Asphalt and Concrete Pavements | Moderate | Good |
Brick Surfaces | Moderate | Good |
Linoleum and Vinyl Floors | Excellent | Excellent |
Applications of TPR and TPE casters
Both TPR and TPE find extensive use across industries, thanks to their unique properties and adaptability. Here’s how each material shines in practical applications:
- Healthcare: Commonly used in medical carts, hospital beds, and equipment trolleys due to their non-marking properties and ability to absorb shocks.
- Retail: Ideal for shopping carts and service trolleys where quiet movement is essential.
- Industrial Settings: Used in warehouses and factories for material handling equipment because they can support heavy loads while minimizing noise.
- Food Service: Suitable for kitchens and food transport carts due to their resistance to cleaning agents and ability to maintain hygiene.
- Hospitality: Employed in hotel service carts and furniture where smooth mobility is required without damaging surfaces.
- Janitorial Services: Found on cleaning carts and equipment. The non-marking feature protects floors while allowing for easy maneuverability in tight spaces.
- Warehousing and Distribution: Used on trolleys for transporting goods within warehouses, can handle moderate loads while providing shock absorption to protect sensitive items during transport.
Both materials continue to evolve, with advancements in formulations opening new doors for innovative applications. Their combined traits of flexibility, durability, and recyclability make them indispensable in modern manufacturing.
FAQs
-
Q: Do TPR and TPE Contain Latex?
A: Neither TPR nor TPE typically contains natural latex. While both materials can mimic the properties of latex in terms of flexibility and elasticity, they are synthetically produced from petrochemical sources or specific polymer blends. This makes them suitable alternatives for individuals with latex allergies.
-
Q: Are TPR and TPE Water-Repellent?
A: Both TPR and TPE exhibit water-repellent properties to varying degrees:
TPR: Generally has good resistance to water due to its synthetic nature, which helps prevent moisture absorption. It is often used in applications where water exposure is a concern.
TPE: Also exhibits water-repellent characteristics, making it suitable for outdoor applications. However, the specific water resistance can depend on the formulation and type of TPE used. -
Q: Is TPR toxic?
A: No. Thermoplastic Rubber (TPR) is safe and widely used in products that come into direct contact with the human body, such as medical devices and children’s toys. TPR is free from harmful substances like latex, phthalates, and heavy metals, adhering to international safety standards. Its non-toxic, hypoallergenic, and durable properties make TPR ideal for safe and reliable applications.
-
Q: Is TPE toxic?
A: No. Thermoplastic Elastomer (TPE) is safe for a wide range of applications, including direct contact with the human body. Its hypoallergenic properties minimize the risk of allergic reactions, making TPE ideal for use in medical devices, personal care products, and children’s toys.
-
Q: What is the classification of TPEs?
A:
Thermoplastic polyurethanes (TPE-U)
Thermoplastic co-polyesters (TPE-E)
Thermoplastic polyamides (TPE-A)
Styrenic block copolymers (TPE-S)
Thermoplastic vulcanizates(TPE-V)
Polyolefin blends (TPE-O)
To gain a deeper understanding of the TPEs classification, click this link.
Questions?
Email us at eric@wheelswaycaster.com or contact us for further information on the ideal caster wheel solution for your equipment.